This project was to create a CNC capability on an old machine that was manually operated. Prior to this project, a technician would retrieve a template and lay it over a panel that was held together by a few manually drilled and installed rivets. The template was coated with blue ink, which was transferred through holes in the template to the panel face. The template was then removed and cleaned. Next, the panel was placed on a roller table where it could be easily moved by hand for precise positioning. The machine operator would sit in front of the operating head of a Gemcor (now Ascent Aerospace) and align one of the dots on the panel with a laser dot on the surface. Once aligned, the operator would hold the panel steady and press a foot pedal which caused the Gemcor machine to drill a hole, insert a rivet, and set the rivet in one action that would take a couple of seconds. The operator would then manually move to the next ink dot and repeat the process hundreds of times to complete a panel.
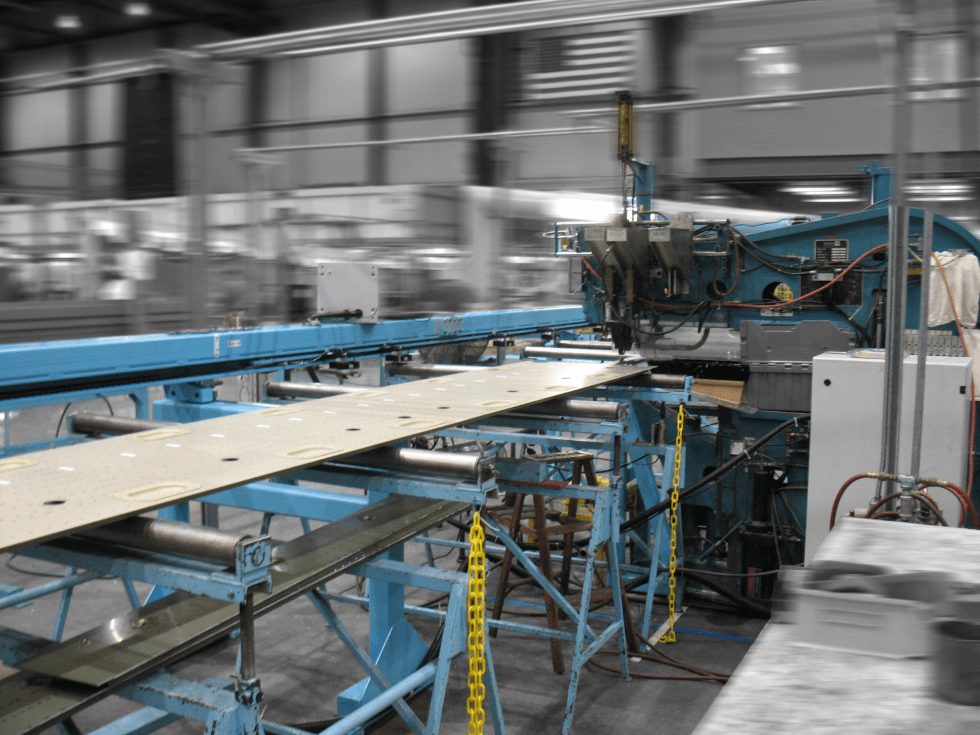
With the automated system operating today, almost all that process has been eliminated. There is no requirement for templates or ink-dotting, and no requirement for an operator to constantly tend the machine. The operator simply takes the pre-assembled panel and slides it into the left-front corner of the positioner and presses the clamp button. The panels are different thicknesses, so the clamps self-adjust to hold every panel correctly. Next, the operator selects which panel is being made and pushes the start button. Depending on panel size, in one to two hours, a panel will be fully assembled. The Gemcor machine was decades old but operated well. This upgrade was around 10% of the cost to buy a new machine that had the same functionality as the upgraded machine.
Delta Sigma integrated the controls of the new positioner with Gemcor machine for seamless operation. There was no CAD data for this part – the panel design was almost 50 years old – so the control system was designed to operate from an Excel spreadsheet. A laser tracker was used to measure the hole positions of each type of panel and that data was dumped into spreadsheets. This allowed for easy user implementation with no CAD or CNC experience required.
The images below show the automation system that was added to the Gemcor system and how it integrated with the existing components. The panel shown in the right image is the maximum size that can be accommodated, and that panel can move anywhere in the work envelope.
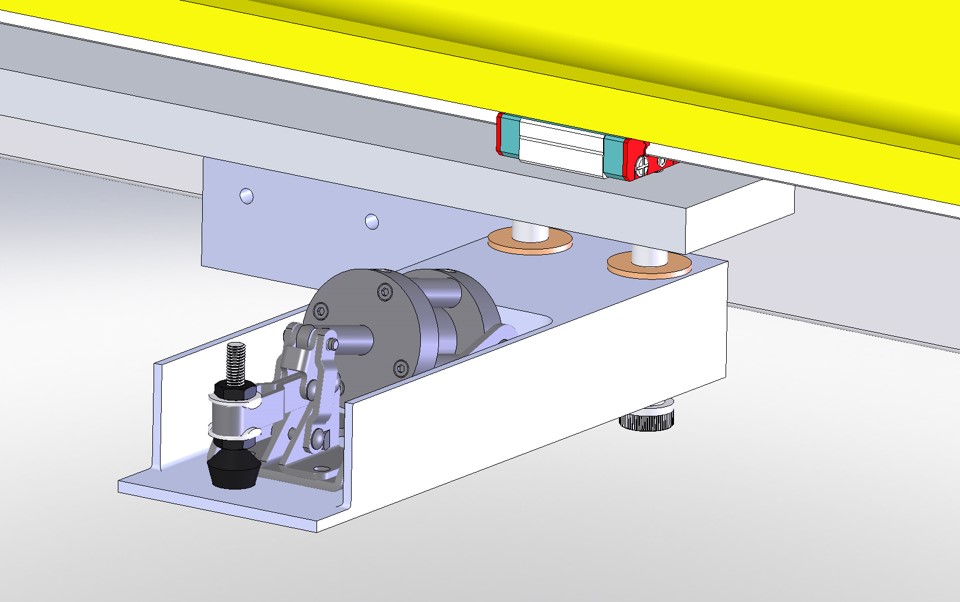
Added Components
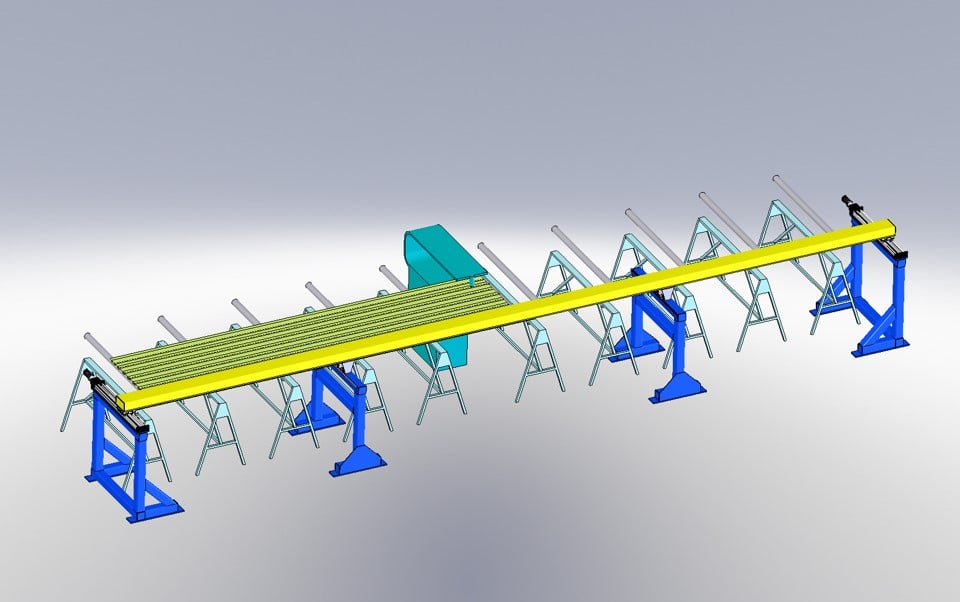
Integrated With Existing System
The system is self-registering. The operator does not have to “inform” the machine where the panel is on the table. The panel to be drilled and filled simply needs to be butted against the X and Y reference edges. A single button sets all the clamps, and the system is ready to start.
The X-Y table is controlled by servo motors and produces accuracy and repeatability far in excess of what a human can do aligning an ink dot with a laser dot by moving a 10-foot by 3-foot panel by hand.
This is an example of how easy it can be to upgrade an old machine’s capability with modern automation. There are great machines still operating today that were made in the 70s, 60s, and even 50s that perform their job as well today as they did new. But modern times call for modern methods to stay competitive. Sometimes building automation around a core manual machine that works well can be a lower-cost alternative.