This project took a long difficult manual drilling process and fully automated it with a CNC system that was built for this purpose. The system design made it easy to load component parts and take out a completed assembly using the existing tooling. The Cargo Ramp Door for this aircraft was roughly 10 feet by 15 feet. The Auto-Drill system designed and built by Delta Sigma runs mostly autonomously to complete the entire process. The tool holder can hold enough tools for the full process.
The Auto-Drill system is composed of a gantry on two long rails that are each built independently. The rail pieces were created as independent units so they could be set in place around the existing tooling without disrupting that tooling. Once the two rail systems were set in place, aligned with a laser tracker, Blooand anchored, the gantry was set atop the rail system and made operational.
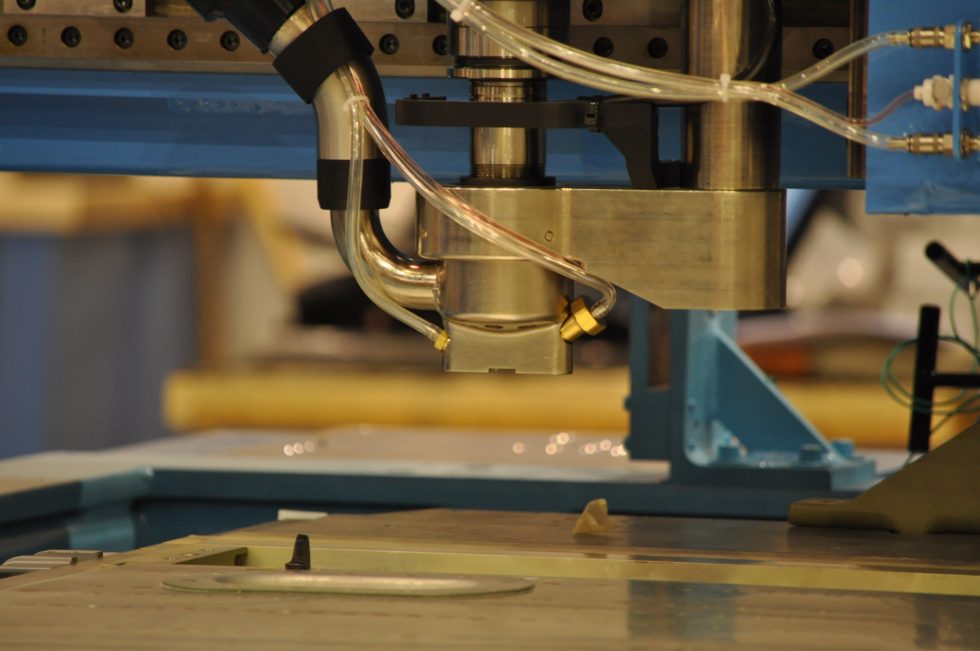
The pressure foot that surrounds the drill bit has several functions:
- Emit an air blast just prior to touchdown to ensure there are no chips in the surface where the pressure foot will touch
- Compress the stack to mitigate interlaminar burrs or chips
- Set the countersink depth
- Contain the cutting lubricant that is applied in extremely small doses during drilling
- Vacuum chips away during cutting
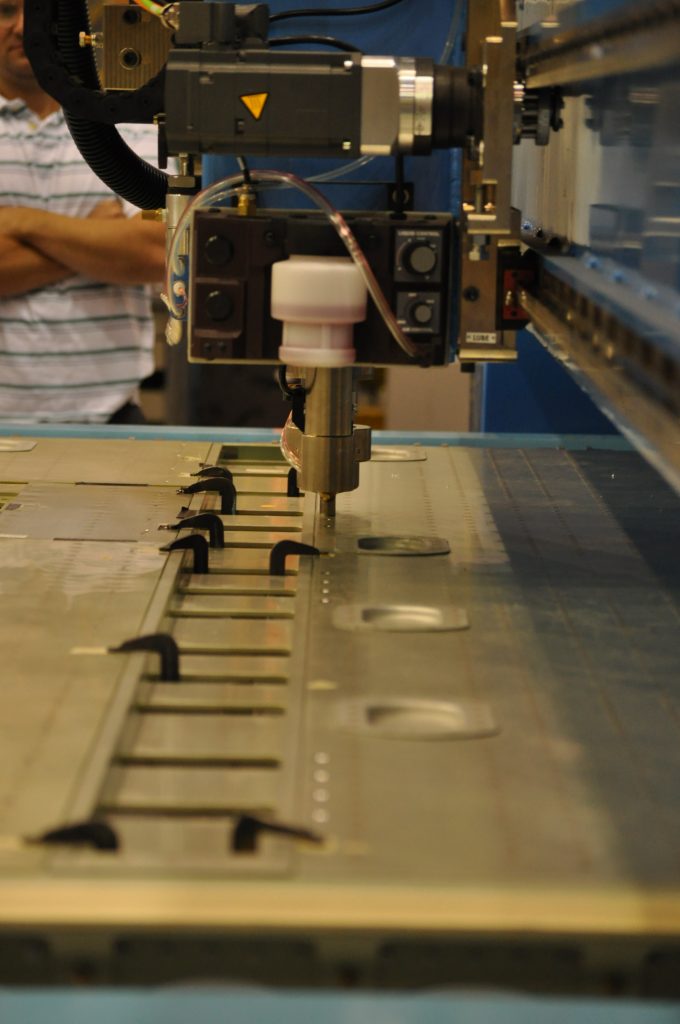
The pressure foot is retracted away from the cutter automatically during tool changes. The pressure foot design in this system provides an intrinsically safe mechanism that ensures that a countersink too deep is not possible. A countersink too shallow (which is correctable) is possible by having a piece of debris stuck to the surface that was not removed by the air blast, although this is an exceptionally rare occurrence. However, it is mechanically impossible to countersink too deep (which is not correctable).
This system drills and countersinks several thousand holes in the Cargo Ramp Door assembly. A built-in coupon check system is included to confirm tool placement in the tool holder prior to the first cut after a tool change. Drilling and countersinking are done in a single pass with two-step cutters.
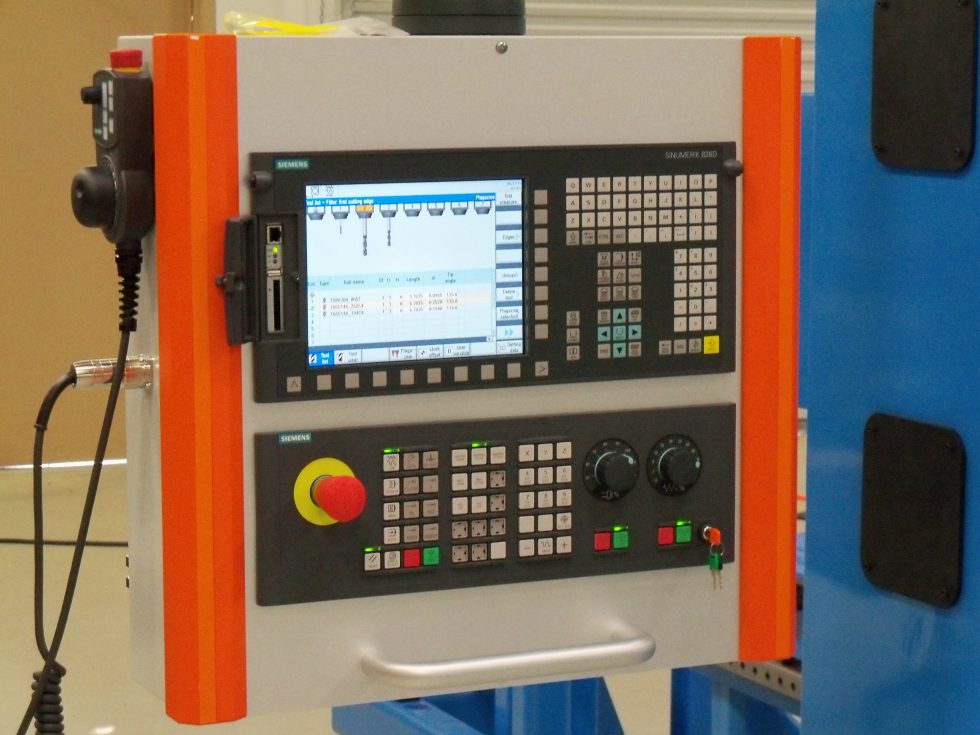
This system drills burrless holes in the aircraft components and runs from standard G-code programming. The user interface is a standard CNC-type control panel.
This is another example where designing and building an automated system that was project-specific as opposed to a generic CNC machine drastically reduced both initial purchase costs and ongoing operating costs by allowing the unaltered use of existing infrastructure in the form of the assembly jig.