This project was to replace a manual drilling process of the primary Wing Beam structural panels of a large Cargo plane from getting one hole per “button push” with an automatic drilling process that completes one wing beam per “button push”, which is about 4,000 holes. Drill time was cut by a factor of 5 (from 5 days to 1).
The Auto-drill improved quality in several ways:
- Drills burrless holes, vastly reducing deburr time
- Eliminated the possibility of missed holes
- Eliminated the possibility of wrong-size holes
The originally planned scope of this project was to replace the 50-year-old tooling with new automated tooling that included the auto-drill capability. DSC proposed that along with an alternate proposal at approximately 10% of the cost that used a portable auto-drill that could attach to the existing tooling and easily move amongst the four wing jigs.
The existing jigs still amply met all the requirements for accurately positioning and securely holding the hundreds of critical parts in place while drilling was taking place. The retrofit was the selected option as having the best business case.
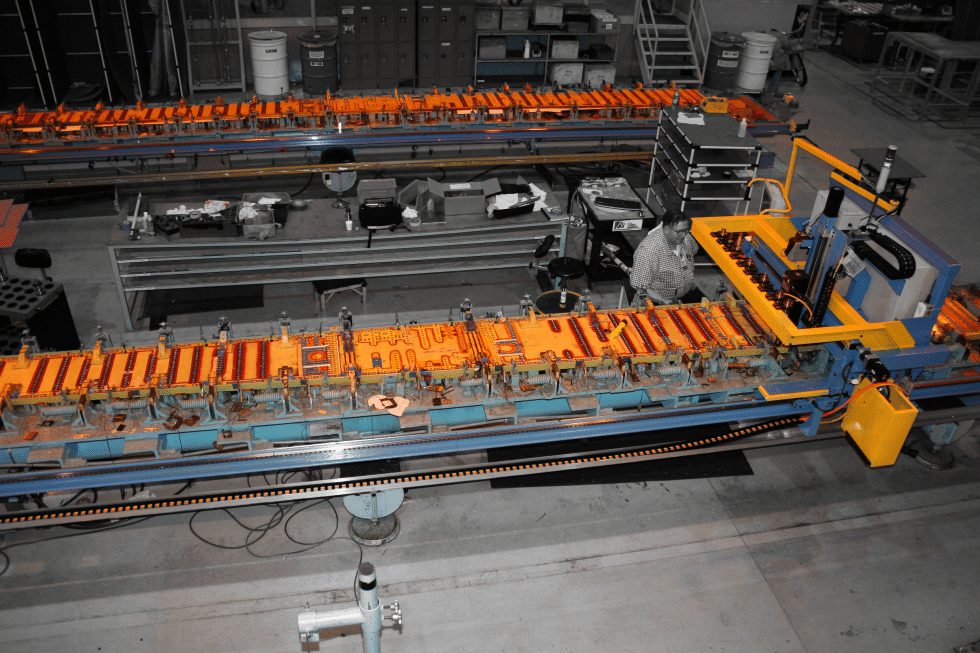
Achieving Accuracy Using Magnetic Encoding
To achieve the needed accuracy in the wing station (along the 50-foot length of the wing), Delta Sigma added SCHNEEBERGER MONORAIL AMS distance measurement rails that use magnetic encoder stripes rather than a glass scale which improves both robustness and accuracy in a cutting environment. These rails were added on one side of each wing fixture.
Friction wheels are used to drive the Auto-drill along the length of the wing fixture. Several durometers of the friction material were tested for slippage and position accuracy. The best compromise was reached and a 0.050” coating on precision machine wheels was used. A drive wheel on each side is used, while the AMS encoder rail provides position feedback to the closed-loop system. Both drive wheels are slaved to a virtual master axis (that is always perfect) to improve response time and eliminate any potential oscillations.
The crossbeam axis is a ball-screw-driven axis. These two axes provide the drill head position to high accuracy. A servo-driven quill axis creates the plunge move. The system uses Siemens servo drives for all axes.
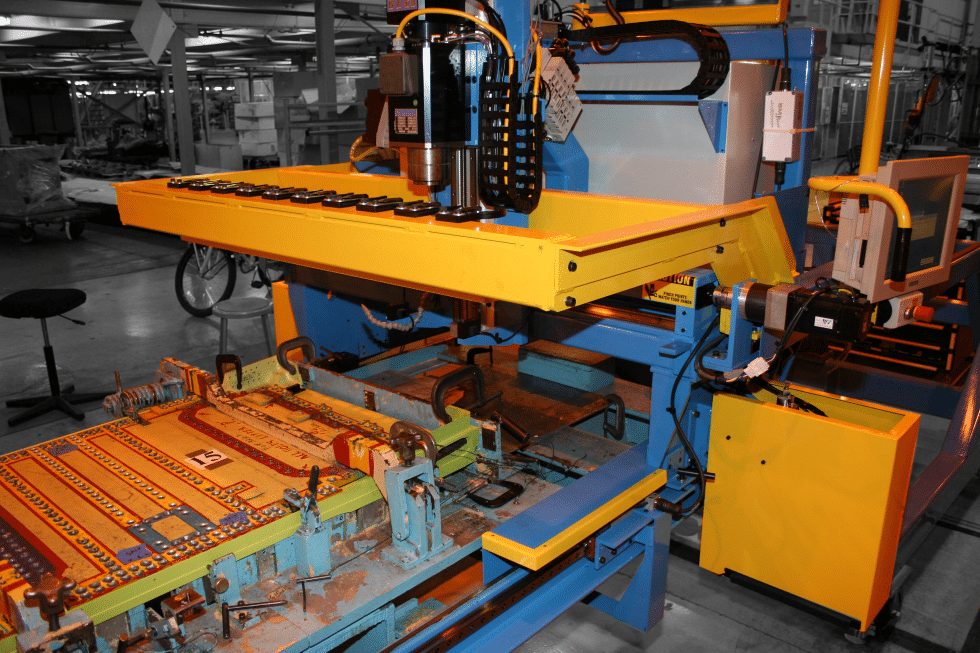
A pneumatic axis moves the 10-place tool changer in and out for automatic tool changes. The system can hold enough tools to cut an entire wing without operator intervention. Each drill bit is measured by an optical measurement system as it is loaded into the tool holder to validate it is the correct size. That measurement system inspects for a broken bit every 10 holes and whenever it is returned to the holder. If a broken bit is detected, an operator is called and a “broken bit” process is executed that goes back to the last inspected hole and moves forward to find where the bit was broken. A “restart” will start the drill machine at either the hole where the bit broke, or the next hole, at the operator’s choice.
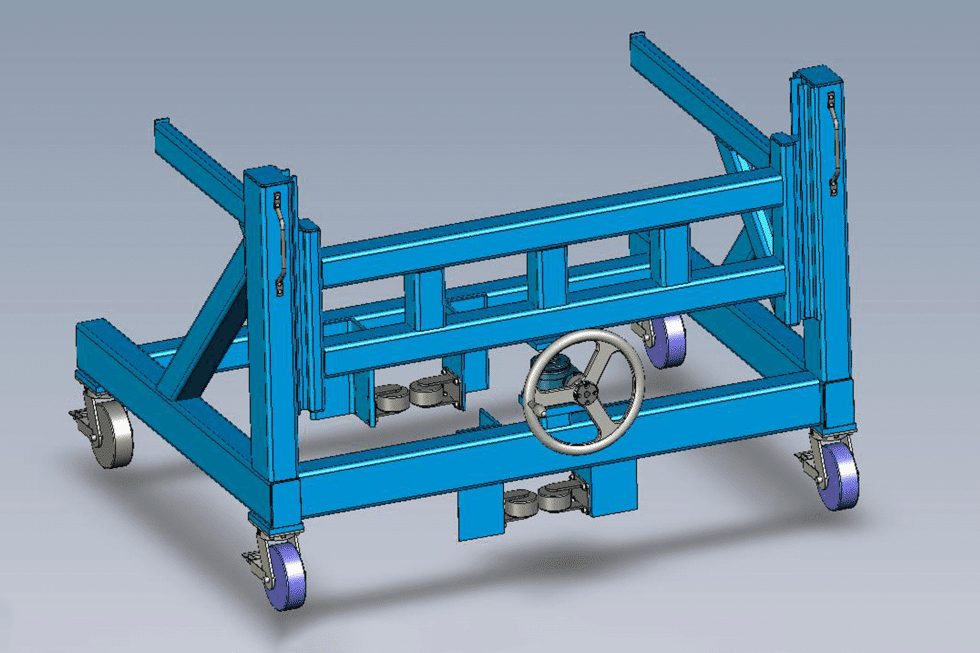
Wing Fixture Utility Integration
Utilities are integrated into each wing fixture. This includes electrical and pneumatic power. The system can run on 208 or 480v 3-phase power. A feature in each power connector tells the Auto-drill which jig it is on. The drill program is automatically selected. A transport cart was supplied to move the Wing-drill between jigs. This transport cart provides storage when the Wing-drill is not in use. This was originally designed with caster wheels but later changed to air-casters to improve ease of alignment when placing or removing the wing-drill on/off the wing jig. The process of placing the wing-drill on the wing jig, removing the cart, attaching the utilities, homing all axes, and being ready to start drilling is less than 5 minutes.
Burrless Holes
The cost to deburr thousands of holes can be considerable. It is difficult to build a system that is 100% perfect at drilling holes that are 100% burr-free. Among the factors that affect the cutter exit quality are:
- Material being cut
- Part-holding steadiness/security
- Cutter speed and feed rate
- Cutter sharpness
- Amount of cutting fluid still of the drill bit just before exit
However, given the above factors are all within their proper parameters, a drilling system built by Delta Sigma can drill approximately 15 holes in 0.125” aircraft aluminum in about 1 minute, and you would not be able to tell which side is the entrance and which side is the exit with zero deburring.